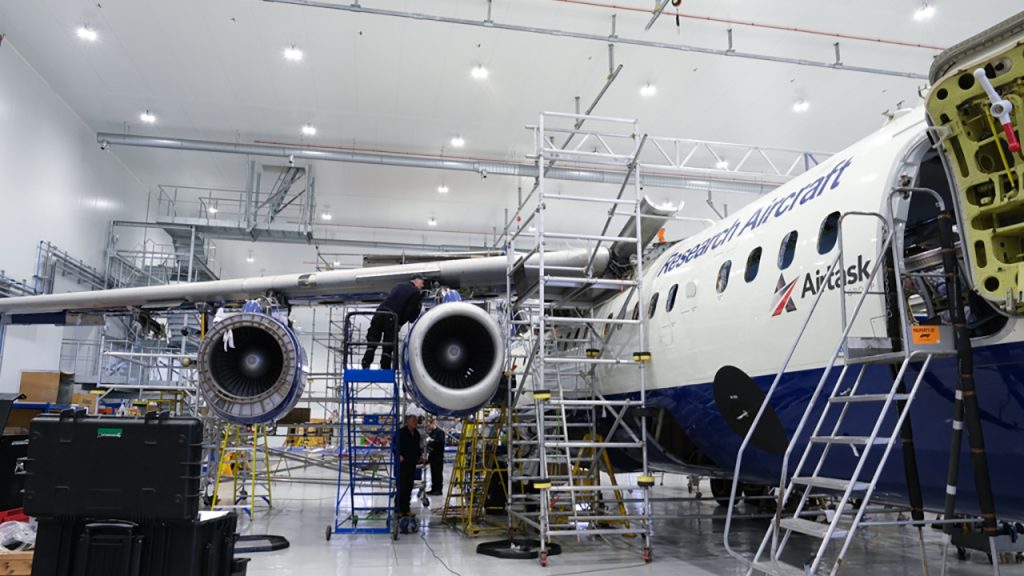
Behind the scenes of our research aircraft’s biennial maintenance inspection
Throughout October and November, the FAAM Airborne Laboratory’s research aircraft is undergoing an extensive inspection, known as a C Check.
The C Check happens every two years and involves removing, inspecting, and replacing all of the aircraft’s components, and takes an estimated 5000 hours.
During this time Avalon Aero’s specialist engineers are also working with the Mid-Life Upgrade team to implement some of the programme’s aircraft infrastructure changes.
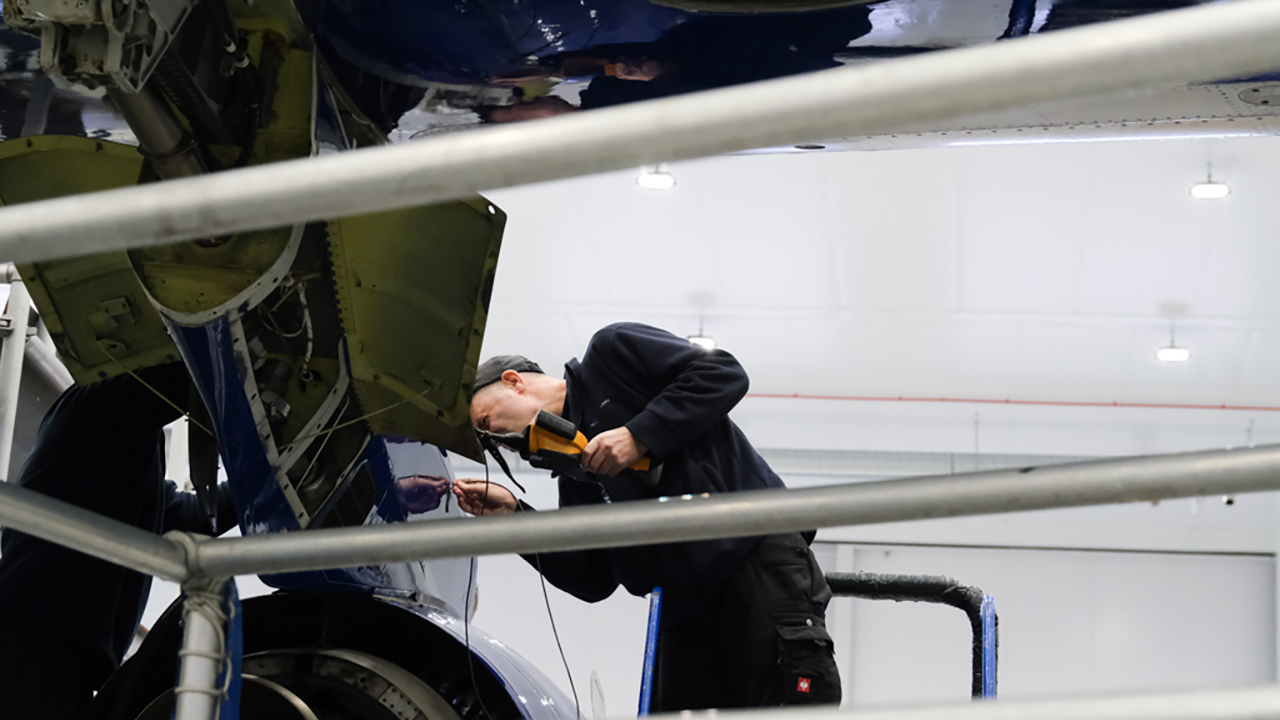
Routine research aircraft maintenance
Our aircraft, despite its age, has relatively few flying hours under its belt. The aircraft is only used for research missions, so its maintenance schedule is optimised for low use.
Checks for functionality and serviceability are carried out weekly, monthly, every three months, every six months, annually, and every two years – for the C Check.
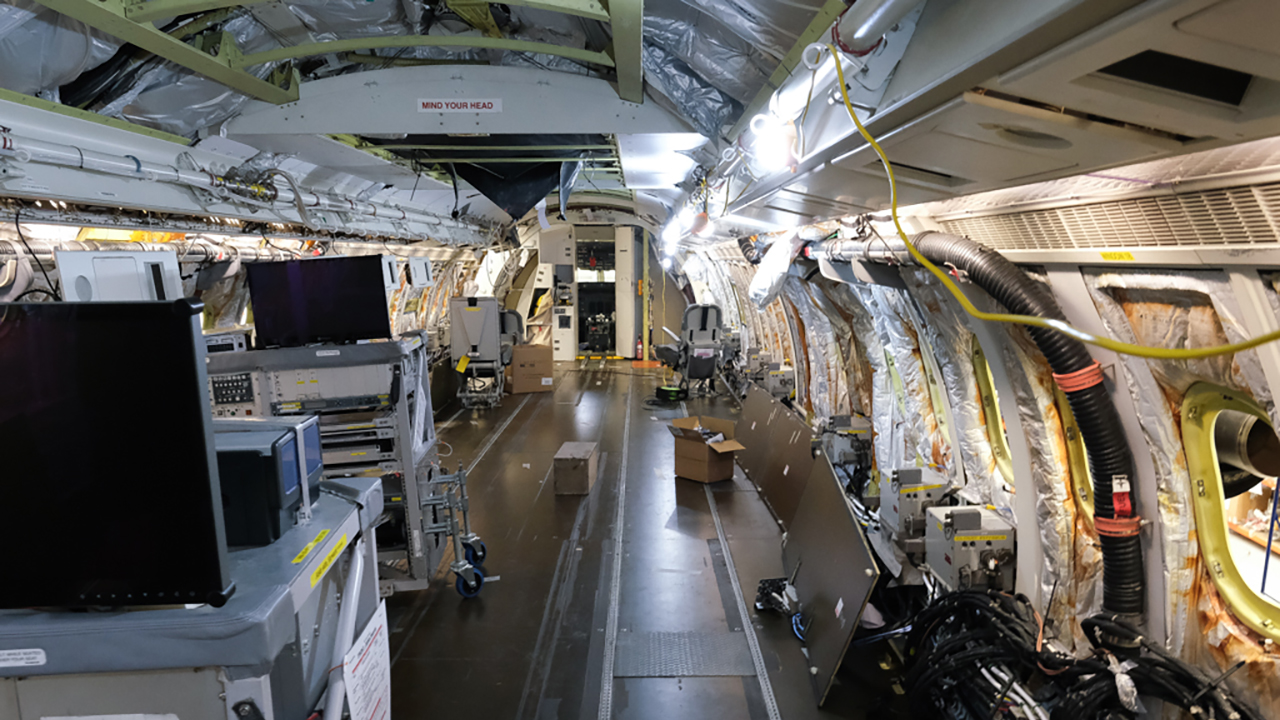
Monitoring stress on the airframe
The FAAM Airborne Laboratory, managed by the National Centre for Atmospheric Science, operates a uniquely modified BAe 146 aircraft. Each flight it undertakes is equivalent to four flights, in terms of the stresses placed on the airframe.
Although the FAAM Airborne Laboratory team has been flying this aircraft since 2003, it had a long history before its conversion to a research facility. Its life began in 1981 as the prototype BAe 146-100, and it is this prototype status and the aircraft’s age that means extra attention needs to be paid to structural integrity.
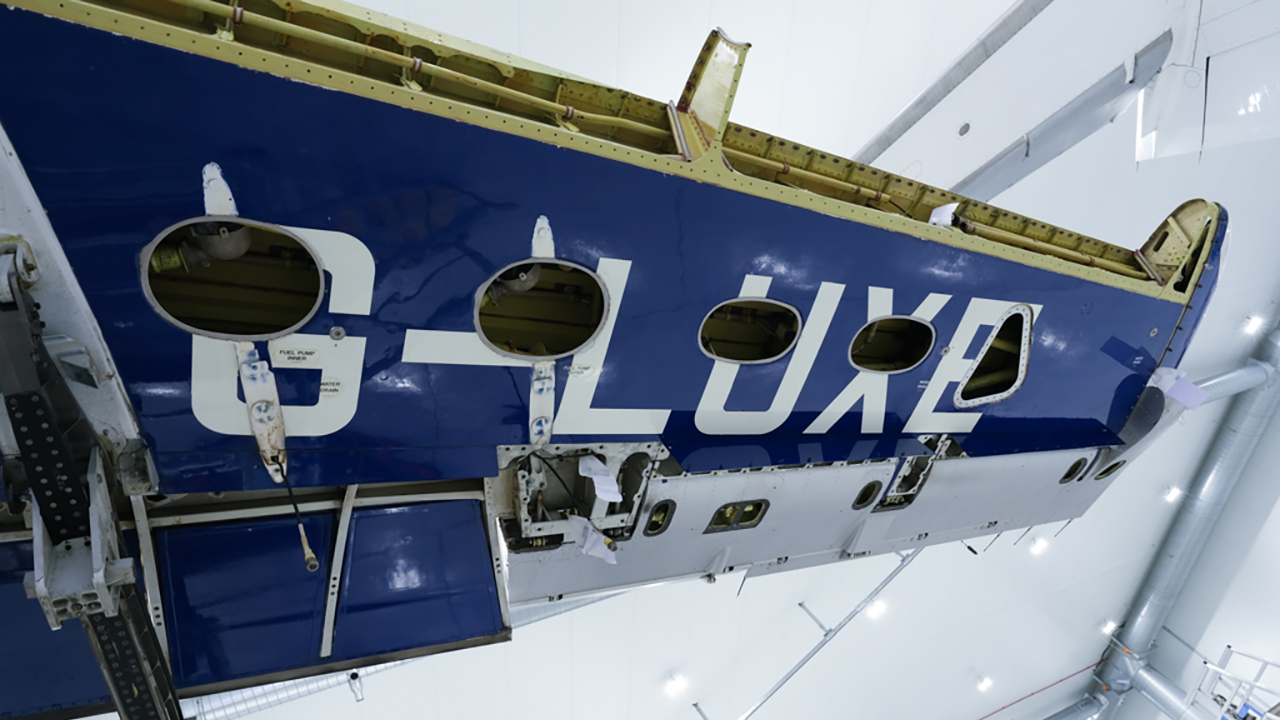
The aircraft has been modified to carry atmospheric research equipment, some of which is fitted to the aircraft exterior – for example the Large Radiation Blister on the fuselage and the instrument pylons under the wings. These modifications change how air flows around the aircraft as it flies, meaning that different stresses are placed on the airframe compared to non-modified BAe 146 aircraft.
We also fly in non-standard ways, with many ascents and descents in a single flight, as well as flying in turbulent conditions. Our lowest-level flying also happens over sea, meaning that our aircraft is at extra risk from corrosion due to spray. During C Check, one of the most intensive inspections is to check for and manage corrosion of the airframe.
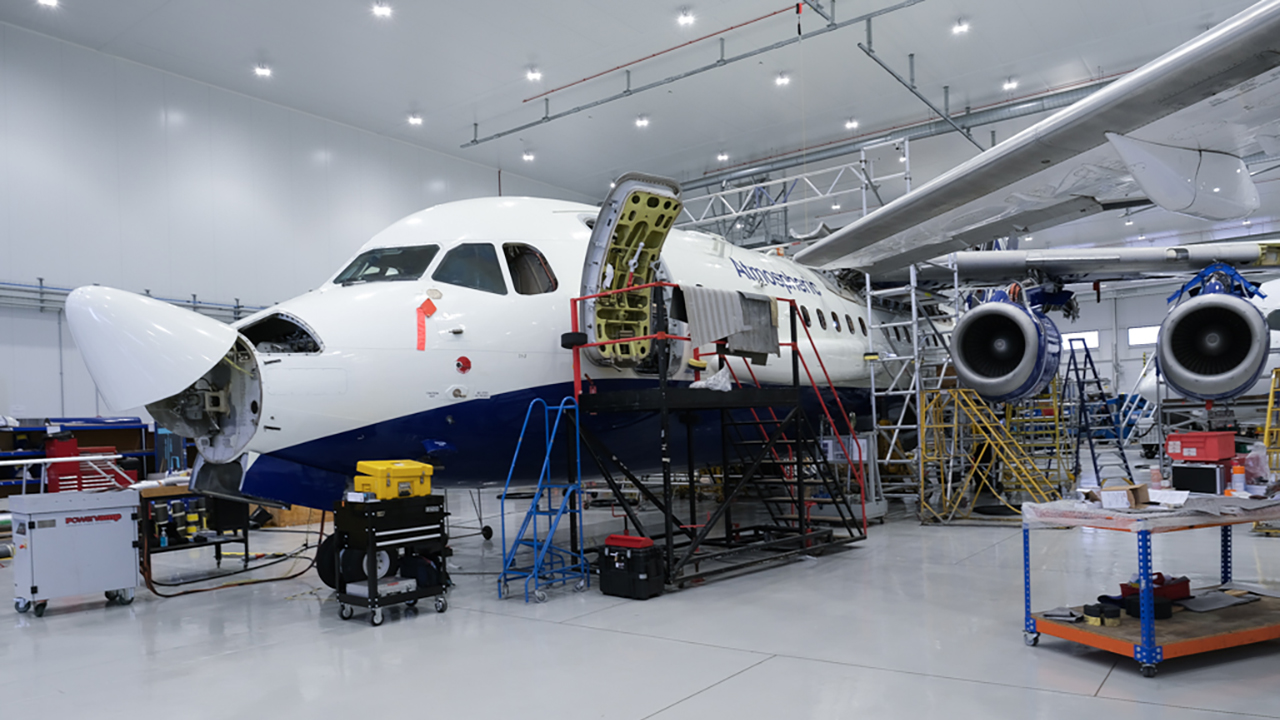
We measure airframe stress through operational load monitoring, using a number of sensors that can tell us how the aircraft is coping with the strain of our unusual flying patterns.
Airframe stress monitoring has allowed our engineers to determine that our research aircraft could be operational out to 2040, when it will be nearly 60 years old.
Making and monitoring future modifications
One of the future modifications in scope, as part of our Mid-Life Upgrade programme, is replacing the existing auxiliary fuel system. Replacing this fuel system will improve how it is maintained and operated.
We are also using the opportunity to increase the capacity of the system and add in flexibility via removable tank designs. Currently there are three fuel tanks situated in the rear hold comprising the auxiliary system, and these will be replaced with four new tanks and supporting systems that will enable the research aircraft to fly further, for longer, and to make more atmospheric measurements.
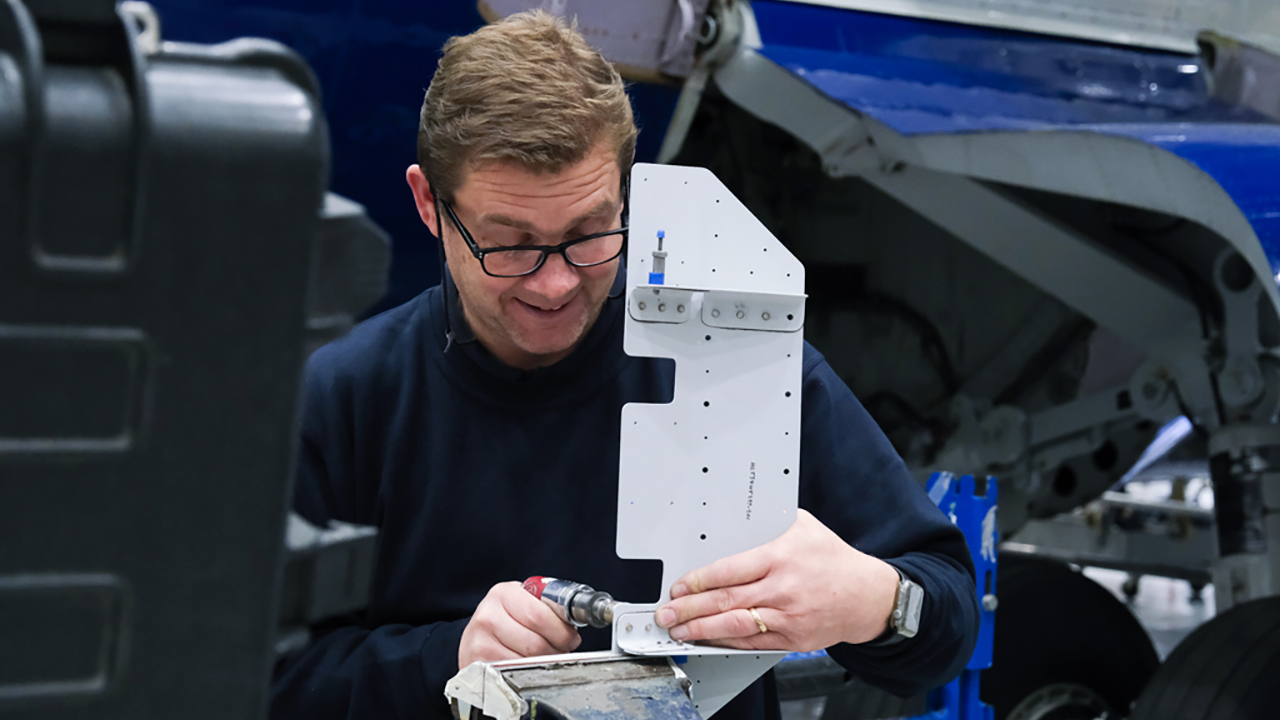
Currently, the space the fuel tank is intended to occupy is partially obscured by a Heimann Radiometer – a thermal camera that can measure ground and sea temperatures below the aircraft as it flies. The pressure box that the radiometer sits in is currently being modified to accommodate a mock fuel tank installation. The mock tank will help the team plan for fitting the new fuel tanks and removal of the existing system.
The Mid-Life Upgrade team is also looking to remove the Whole Air Sample system on the aircraft, and the associated pipework and electrics. Removal of redundant equipment like this will help to take weight out of the platform and potentially free up space for new equipment.